Remote wireless sensors used to rely on battery power to measure data and send it wirelessly. When the wireless sensor node is in the reach of personnel, the battery can be replaced by human resources. This method is reliable but sensitive. The useful life of the device will depend on the battery life, and the typical battery life is about 5 to 10 years, which is expensive.
In some applications, it is difficult to charge the battery, and the cost of manually charging the battery is high. For example, charging a wireless sensor battery in a nuclear power plant, a refinery, or even an underground facility may be quite expensive; if a larger battery is used instead Longer life is available, but when the size is larger, the cost is higher. As a result, how to make the battery last longer is an important issue.
Provide additional power energy harvesting to reduce battery dependence
Energy harvesting provides a possible solution to the problem of extending battery life. When the collectable energy is available, the sensor node is powered by the energy; when there is no energy to be collected, the main battery is used to power the sensor node. Of course, energy harvesting is not a new concept. The first hydroelectric power plant that used water and gravity to drive turbine generators was built in 1882 to provide green energy and a sustainable source of electricity. It is a large-scale energy harvesting. However, because this energy is highly dependent on natural terrain, a large, expensive transmission network is required; at the same time, transmission loss will increase as the distance increases, thus significantly reducing the available power.
However, in many cases, the wireless network sensing node requires only a few milliwatts (mW) of power, so a smaller energy harvesting solution can be used, which is compact, wireless, and in power spectrum. Low-end application power supply.
Although non-conventional power supplies such as solar cells (photovoltaic cells) and piezoelectric transducers are well known, it is still challenging to use such unconventional power supplies; such power supplies require specific power conversion circuits for high efficiency. Collect, manage, and convert energy into electrical energy to power sensors, microcontrollers (MCUs) and wireless transducers.
No matter when the power supply voltage is higher than the required voltage, it must be stepped down to the available voltage, or in some cases, it must be rectified first, then step-down conversion, which requires a specific energy harvesting circuit. This type of circuit is a very complex discrete circuit with up to thirty components and must provide high efficiency for practical use. Until recently, specialized energy harvesting power integrated circuits (ICs) emerged that combined with appropriate transducers to create a compact, simple, and highly efficient power conversion and management solution.
Ultra low power applications are available for a variety of wireless systems such as transportation, infrastructure, industrial inspection, building automation, asset tracking and more. This type of system is usually in standby mode (sleep) and only needs a few microwatts (W) of power to maintain operation; after the system wakes up, the sensor measures parameters such as pressure, temperature or mechanical deflection to wirelessly transmit data to the remote system. Manager; the total time taken to measure, process, and transmit is typically only a few milliseconds (ms), but tens of milliwatts of power is required in a few milliseconds. The working period of the above applications is usually very short, so the average power that must be collected can still be relatively small.
Although the power supply may be just a battery, it must be replaced manually; if an environmental energy-based energy harvesting design can be used, and the battery is used when no environmental energy is available, the battery life can be greatly extended.
Take the building's automated wireless sensor system as an example. Its system of position sensors, thermostats, and light-sensing switches eliminates the power or control wiring that is generally required, but the environmental energy that is collected through energy harvesting. The battery, which is used to power the wireless network, does not require cable installation at the outset. This alternative does not require routine maintenance of the cable system, further saving money.
In addition, the wireless network using energy harvesting technology can also be connected to the internal sensor of the building. When there is no one in the building, the system automatically turns off the power supply in the non-essential area to reduce heat, ventilation and air conditioning (HVAC) and lighting costs.
An energy harvesting-based HVAC monitoring system, such as a forced air flow duct in an industrial park that continuously monitors air flow speed, temperature, and pressure; all wireless sensing nodes may have built-in temperature, pressure, and air flow sensors The measurement is taken every 5 seconds. Because HVAC systems are distributed over long distances and are often buried in the infrastructure of the building, the cost of erecting power and information transmission cables is very high, and the cables need to be maintained from time to time, which is also a huge expense.
The cost of regular battery replacement is very high, as each battery must be hired by someone. The solution is to construct a continuously operating power system that uses the collected ambient energy when ambient energy is available; when no ambient energy is available for collection, it is battery powered to minimize battery drain.
One of the most common and easily accessible environmental energy sources is vibration. Small piezoelectric transducers convert the vibrational energy of a HVAC compressor into a small current alternating current (AC) electrical signal (Figure 1). This collection of energy needs to be rectified and stepped down to provide a usable low voltage to power the wireless sensing node; its battery can be used as a backup power source, which can be used when there is no time to collect energy, which can effectively extend battery life.
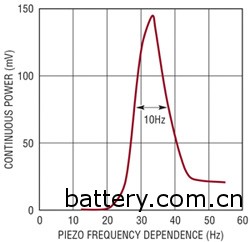
Figure 1 The power provided by a small piezoelectric transducer varies with the piezoelectric frequency.
[@B]Energy Harvesting IC Integrated Dual Power Source [@C] Energy Harvesting IC Integrated Dual Power Source
There are currently energy harvesting voltage regulation solutions available on the market that provide up to 50 milliamps (mA) of continuous output current when harvesting energy is available, thereby extending battery life. The IC does not require a battery to supply current when it is powered from the collected energy source. When powered by the battery under no load, only 750 nanoamperes (nA) of operating current is required.
The new generation integrates a high-voltage energy harvesting power supply and a synchronous buck-boost DC-to-DC converter; the converter is powered by the main battery and produces a single, uninterrupted output for energy harvesting applications commonly found in wireless sensing nodes. The energy harvesting power supply consists of a full-wave bridge rectifier suitable for AC or DC input, and a high efficiency buck converter that collects energy from piezoelectric (AC), solar (DC) or magnetic (AC) sources; main battery input Powering the buck-boost converter, when no harvest energy is available, the converter operates from an input voltage range of 1.8 to 5.5 volts to allow immediate adjustment when the input current is above, below or equal to the output current. At the same time the device will automatically switch to battery power (Figure 2).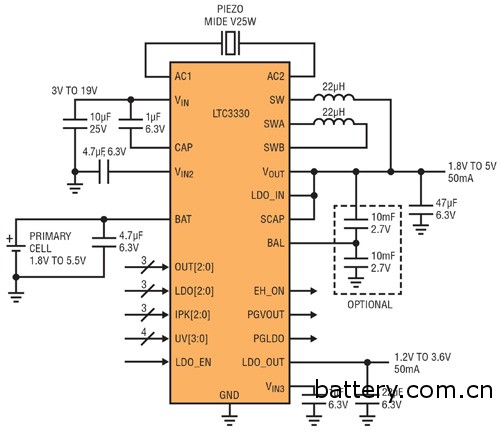
In general, the relevant application may use the DC input on the AC1 side of Figure 2, and it is possible to use the second input on the AC2 side at the same time, or a single AC input connected across AC1 and AC2. If the energy harvesting power source is an AC power source, such as a power source generated by a piezoelectric transducer, the energy harvesting regulator chip will provide a DC voltage to the input capacitor through an integrated full-wave bridge rectifier; DC energy is directly stored. In the input capacitor, once the voltage on the input capacitor exceeds the undervoltage lockout (ULVO), its input priority sequencer turns off the battery and regulates the output from the acquisition supply. The output voltage (VOUT) is configurable from 1.8 to 5 volts and is typically powered by a radio frequency (RF) transceiver.
In addition, the 1.2 to 3.3 volt linear regulator (LDO) output has low noise and is typically used as a microprocessor core supply. When using an energy harvesting power supply, these two outputs combine to provide up to 125 milliamps of output current; when the battery is turned on, it provides 50 milliamps of current. In the energy harvesting mode, if there is excess output power, there may be a super capacitor for future use, which further extends battery life. The built-in supercapacitor balancer is used to further optimize energy storage; where the quiescent current of the battery is zero when using the energy harvesting power supply, all battery energy is saved for future use.
If the energy harvesting regulator has a built-in full-wave bridge rectifier, it is suitable for AC input generated by piezoelectric or magnetic transducers, and rectifies the AC signal into a DC signal; if there are multiple transducer inputs, it will be used. The one with the highest available voltage (power).
The input current is collected through the input capacitor. When the ULVO threshold can be set, the priority sequencer turns off the battery, and the synchronous buck converter supplies the required power to the output; the power is transmitted through the VOUT pin or low noise. The LDO output is provided to the load, and any excess power is stored in the output capacitor and/or super capacitor. In this state, the quiescent current drawn by the battery is zero.
The input protection shunt circuit provides safety for voltages above 20 volts. If no energy acquisition input power is available, the priority sequencer automatically switches to the synchronous buck-boost converter to provide the desired output. VOUT and VLDO remain stable throughout the conversion, providing the required power for the sensor, wireless transmitter, and microprocessor.
The buck-boost converter provides 1.8 to 5.5 volts of input voltage and is suitable for a wide range of lithium-ion batteries. The buck-boost converter provides a constant voltage with an efficiency of more than 90%, regardless of whether the battery voltage is above, equal to, or below VOUT. Compared with the general step-down design, the buck-boost architecture extends the battery execution time by more than 30%. When operating through the battery, the total output current depends on the input voltage (VIN) / VOUT ratio, and when the battery is not available. At the final voltage, this output current is approximately 50 milliamperes.
VOUT is the input to the low noise LDO output. The output range is 1.2 volts, 50 millivolts below VOUT. It is pin-configurable and is suitable for powering multiple microprocessor/controller cores. Both VOUT and VLDO have a power good state output to reduce the overall system workload. In addition, the optional supercapacitor balancer ensures the longest life of stored energy.
Double standby battery life only twice
To be precise, how much battery life can be extended depends on the nature of the environmental energy, availability, and the total power required by the wireless sensing node.
In the previous example of HVAC, if the compressor continues to operate, the entire system is powered by the piezoelectric energy harvesting power supply, and the battery is only used as a backup power source. When it is used in the event of power outage or compressor overhaul, then it can be used indefinitely. Extend battery life. For example, in train applications, sensors are used to measure hub bearing temperature, cargo inventory, or temperature; when the train is running, the piezoelectric energy harvesting power supplies the system; when the train is stationary, it is powered by the battery. The above method will greatly extend battery life, which is especially needed for rail vehicles.
Another example is the solar energy energy application. By using solar cells as an energy harvesting power source, the system can operate through solar cells during the day, while also storing excess power in the output capacitors and supercapacitors; when no solar cell input is available The system then discharges the output capacitor and supercapacitor for a few hours before switching to the battery. Depending on external conditions, this may extend battery life by at least twice.
As for how much battery life can be extended, the answer is depending on the situation, but the extension time is between two and indefinite, and the height depends on the system design and I/O power duty cycle ratio. Obviously, it is only possible to extend battery life by incorporating energy harvesting power into the energy harvesting IC and supplementing the energy harvesting power supply with the main battery. In most cases, this also allows designers to use smaller, cheaper batteries. For a variety of wireless sensing node applications, adding a suitable environmental energy transducer and energy harvesting power management IC can significantly extend the system's main battery life. When harvesting energy is available, the IC provides high-efficiency energy with zero battery leakage, making it a very compact and easy-to-implement solution. Through these solutions, battery life can be extended indefinitely in many applications, thus allowing the use of smaller, lower cost main batteries and reducing battery replacement costs.
Agricultural Machinery Parts is general Outlines that is associated with agricultural production machinery parts, which is very wide.
Agricultural machinery parts is general Outlines that is associated with agricultural production machinery parts, which is very wide.Such as: tractor machinery parts, tires, car bucket, harvesting machine including potato harvester, peanut harvester, agricultural machinery and implement of (pears. Rake. Seeding) to plough, for example, plough disc plough, furrow plough, animal plough, part of the whole machine including point, plough leg, plough share, plough blade, etc.The related industries, and form a complete set of product accessories can be called agricultural machinery accessories.
Agriculture Machinery Parts,Aluminum Die Casting Agriculture Part,Mower Housing,Agriculture Parts
NINGBO ZHENHAI BOLANG METAL PRODUCT FACTORY , https://www.diecastingdie.com