I. Introduction
The press brake is a virtual machine in the sheet metal bending industry, but its price has deterred many metal manufacturing practitioners. Therefore, many people choose to DIY their press brakes for reasons of cost savings or manual hobbies.
However, in addition to proficient metal processing and welding skills, it is also necessary to understand mechanics and machine design when manufacturing an entire press brake by oneself.
Before launching this plan, you can search for DIY tutorials online and determine the difficulty of the project based on the teaching videos.
Then, you must develop a detailed manufacturing plan, including the required materials and tools, manufacturing steps, and necessary safety measures, especially when using heavy machinery and welding equipment.
In addition, many important aspects need to be paid attention to, including the quality of materials and tools, tonnage selection, and the range of stroke for the backgauge.
After the press brake is manufactured, regular inspections and maintenance are required to extend its service life and ensure the machine's effective operation. Including hydraulic system, ram, electrical system, foot pedal, etc.
This article will discuss in detail how to build your press brake and the maintenance issues of the press brake in the later stage. Here is a short video for you to watch:
II. What is a Press Brake?
Firstly, let's understand the function and components of a press brake. A press brake is a machine used to bend metal plates into workpieces.
The most widely used driving power system now is the hydraulic system, and electric systems are also increasingly being put into use. The bending force exerted by the driving power system is also known as tonnage, which determines the hardness and thickness of the sheet metal that can be bent.
The frame of the press brake is made of sturdy steel plates and connects all components together, including left and right hydraulic cylinders, ram, workbenches, etc.
The ram of the press brake is a component that can move up and down, driven by a hydraulic cylinder or an electric motor to move the ram up and down. Drive the punch to apply hydraulic pressure on the metal sheet on the lower die and perform bending.
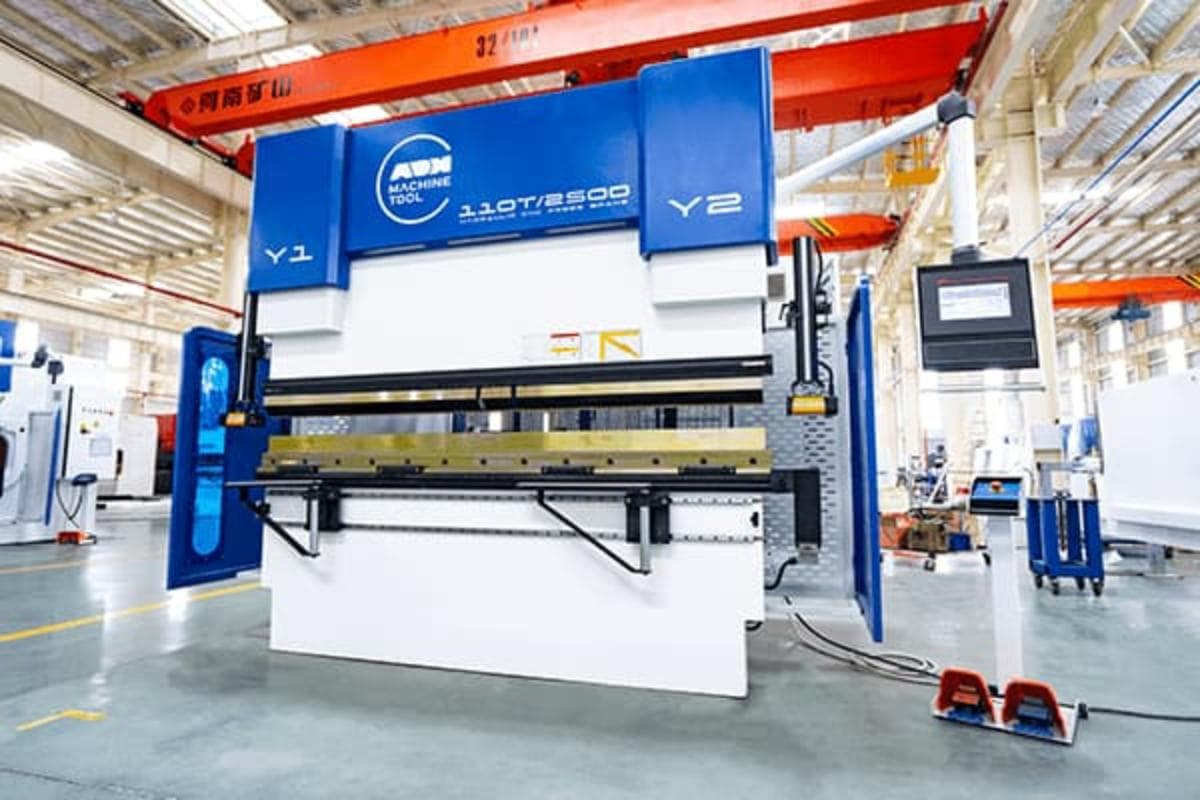
The back gauge of the press brake is used to position the metal plate during bending to ensure the accuracy of bending. The back gauge can be manually adjusted or automatically adjusted through the control system.
The control system of the press brake is a computer programming system that can control the bending process by setting different parameters, and can also perform automatic bending.
III. Materials and Tools Needed to Build a Press Brake
1. Materials
You need to prepare materials and tools for the DIY press brake. Choose a press brake design solution that suits your production needs. It can be manual, hydraulic, electric, etc.
The materials prepared for the construction of the press brake, including steel plates, steel pipes, angle steels, etc., and the steel required for the manufacturing of the press brake frame must be strong and stable enough to withstand the pressure of the hydraulic cylinder.
Other components include hydraulic cylinders, hydraulic pumps, motors, control systems, accessories, valves, back gauge, clamp, press brake tooling (punches and dies), nuts, screws, and various fasteners, etc,
The hydraulic pump provides pressure to the hydraulic cylinder, so the pump's performance needs to be strong enough.
Correspondingly, the hydraulic cylinder drives the ram to apply pressure to the metal plate, and a sturdy hydraulic cylinder can provide significant bending force.
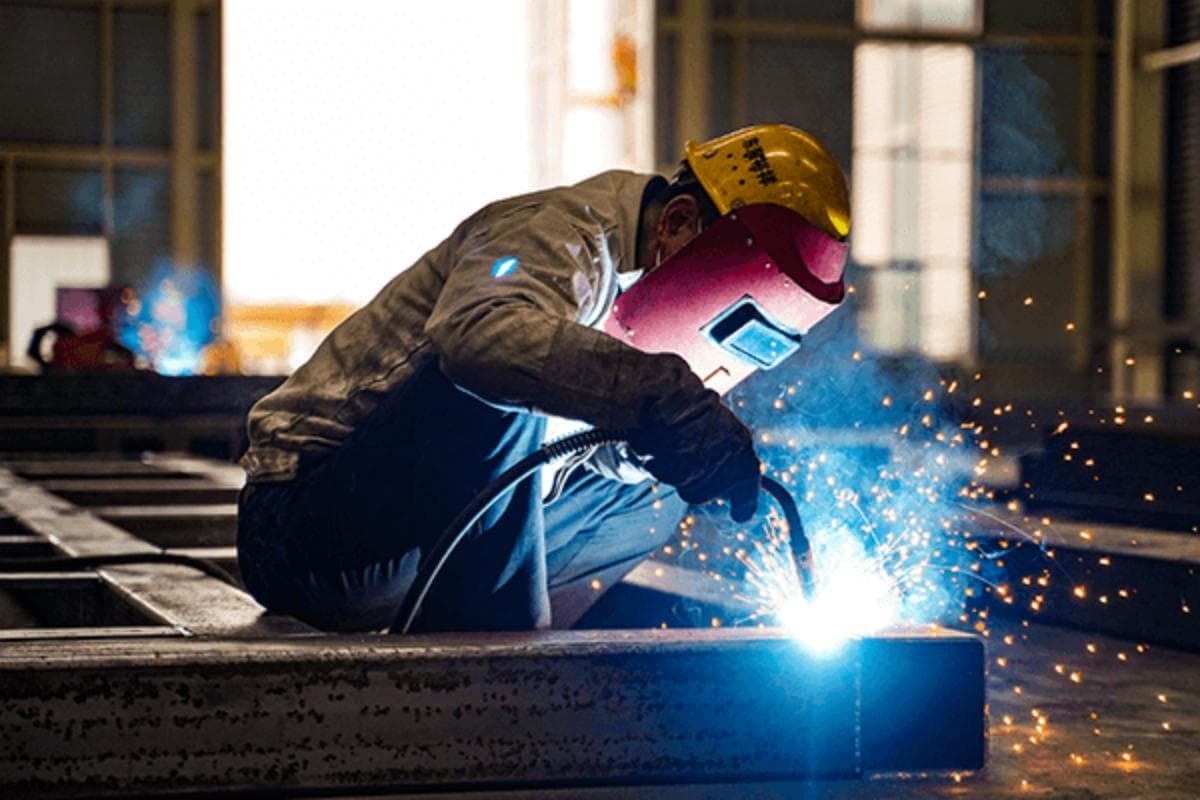
2. Tools
Of course, you also need to prepare some tools to help manufacture the frame and install various press brake components.
These tools include welding machines, drilling machines, cutting torches, and angle grinders, as well as some simple tools such as wrenches, pliers, hammers, measuring tools, etc.
A cutting torch is a cutting tool that can be used to cut metal. Welding machines are used to connect frames and other components together, drilling machines can be used for drilling holes, and angle grinders can be used to polish metal plates, rough surfaces, and edges of holes.
In addition to the above materials and tools, pay attention to the use of personal protective equipment, such as welding helmets, gloves, goggles, etc., and need to be in a ventilated special work area.
The DIY press brake requires a certain investment of time and money, and before starting the project, a budget and manufacturing plan need to be established.
Choosing the appropriate materials, components, and tools is crucial for manufacturing a high-quality and durable press brake.
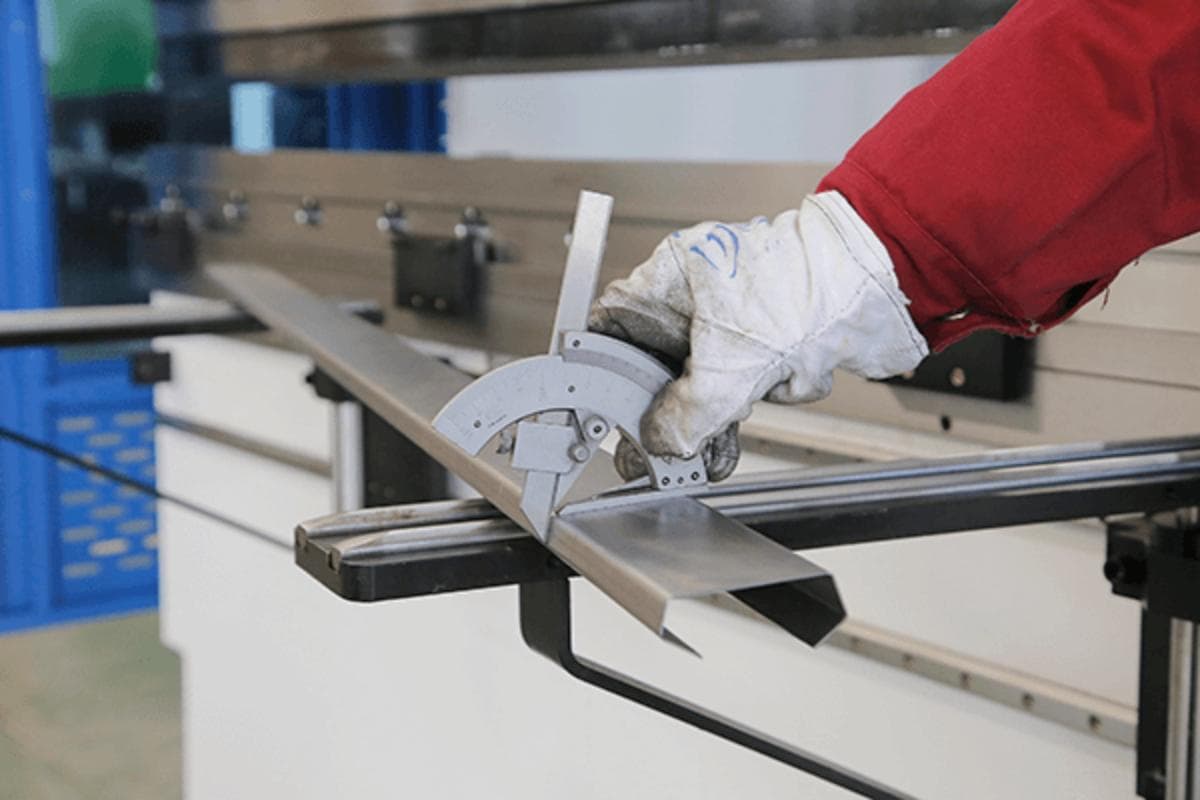
IV. Designing Your Press Brake
There are several important points to pay attention to when designing a DIY press brake. Ignoring any one point can lead to quality issues with the press brake.
Firstly, determine the power source of the DIY press brake, which can include manual, mechanical, hydraulic, electric, etc. Choose the appropriate driving method according to your production needs and budget.
Hydraulic and pneumatic press brakes require the preparation of hydraulic and pneumatic components, including hydraulic cylinders, hoses, fittings, valves, and hydraulic pumps. The manual press brake requires a lever and linkage system for manual operation.
CAD software can be used to design the frame of the press brake, accurately calculate the size of the frame, and the distance between the lower and upper dies, and ensure sufficient space for placing metal plates.
The upper and lower beams need to withstand the maximum bending force, so they need to be very sturdy. Safety protection devices, limit switches, emergency stop buttons, and other components are necessary to ensure the safe use of the press brake.
V. Choosing the Right Components
When selecting the components of a press brake, it is necessary to choose according to one's own needs, but the basic frame must be made of high-quality materials. Taking a hydraulic press brake as an example, let's see how to select some important components.
1. Frame
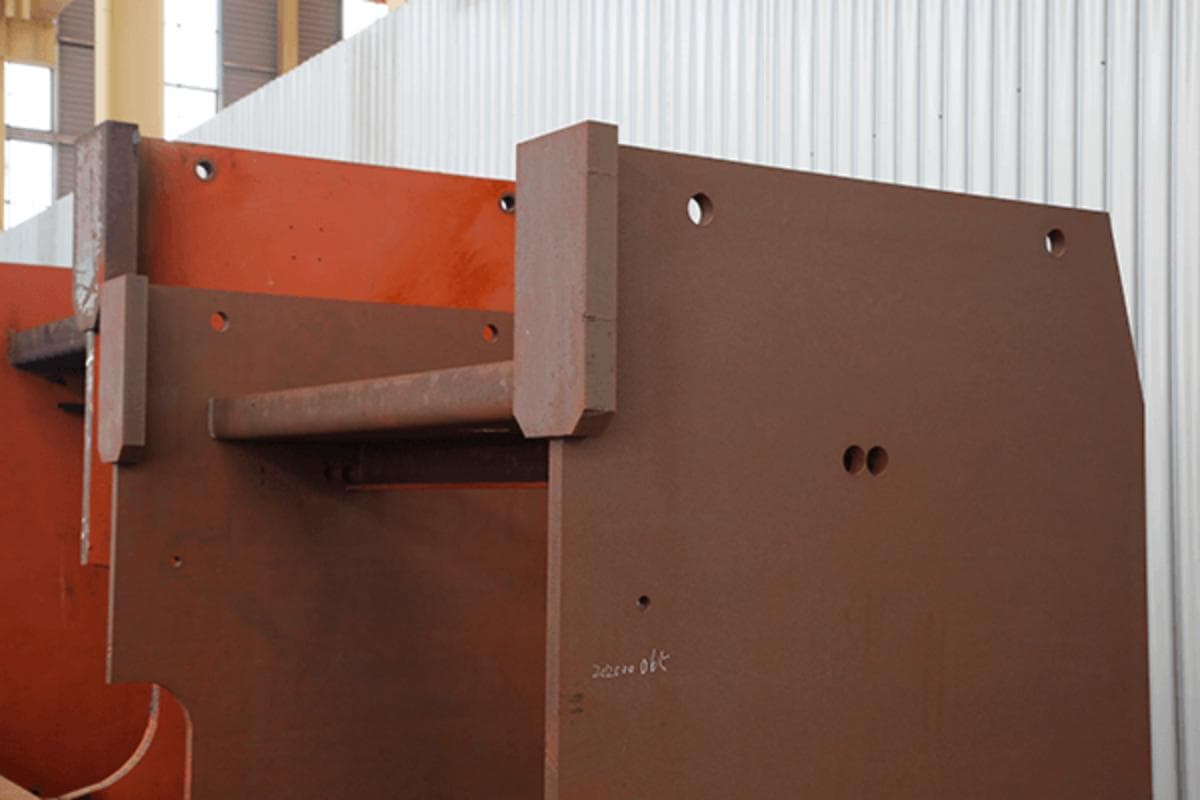
The frame of the press brake needs to be made of sturdy steel structure to support the tonnage during bending. Choose a frame of the appropriate size, which will not occupy too much space and is also sufficient for bending metal sheets.
The stability of the frame is also a consideration, as it needs to be firmly fixed to the ground without shaking or tilting.
If your press brake needs to move frequently, you also need to consider the weight of the frame material, which should be sturdy and easy to handle. Safety functions such as protective devices and emergency stop switches also need to be configured on the frame.
2. Hydraulic Cylinder
The hydraulic cylinder is an important component of the press brake, which is the power source for the press brake to achieve bending. When selecting a hydraulic cylinder, pay attention to the following points.
The rated load capacity of the hydraulic cylinder cannot be less than the maximum tonnage of the press brake, which depends on the thickness, width, and tensile strength of the bending material.
If the bending tonnage exceeds the rated load range of the hydraulic cylinder, it will cause damage to the hydraulic system. The hydraulic cylinder needs to have sufficient stroke length to allow the slider to move up and down extensively during the bending process.
We also need to consider the corrosion resistance and sealing performance of the hydraulic cylinder, as well as its compatibility and reliability with the press brake.
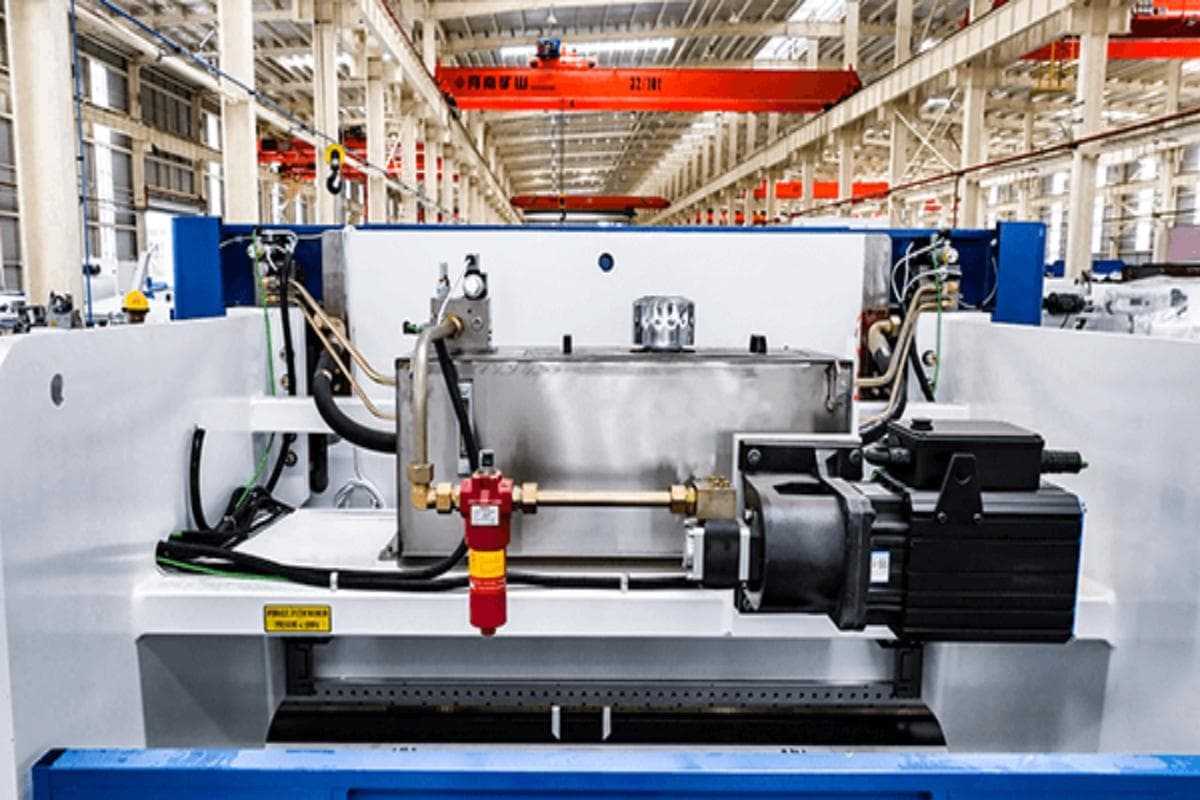
3. Hydraulic Pump
There are different types of hydraulic pumps, including piston pumps, gear pumps, and vane pumps. Choose the appropriate hydraulic pump according to your needs. The power supply of hydraulic pumps is generally provided by electric motors.
When selecting a hydraulic pump, it is necessary to consider the pressure requirements. The hydraulic pump needs to deliver hydraulic oil to the cylinder, and sufficient pressure and flow are required to ensure the oil volume of the hydraulic cylinder.
The pressure and flow rate of the hydraulic pump still needs to be determined based on the tonnage, size, and type of the press brake. The larger the size, the greater the pressure and flow rate required.
VI. Regular Press Brake Maintenance Work
1. Regular Cleaning and Lubrication
Regular inspection and maintenance tasks of the press brake can extend its service life, ensure the normal operation of various components of the press brake, and ensure the accuracy of bending.
After prolonged use, the outer surface of the press brake will accumulate a lot of dust and oil stains, and the outer surface of the hydraulic cylinder will also leak a lot of oil stains.
Long periods of non-cleaning can lead to rusting of the external surface of the machine, abnormal operation of components, and, in severe cases, even damage. Some specific press brakes come with a hydraulic tool clamping system.
Therefore, in order to extend the service life of the external surface of the press brake, it is necessary to regularly clean the external surface, keep the tooling clean, and wipe or clean the body with a soft cloth and cleaning agent.
After cleaning the machine, it is necessary to apply lubricant to some components, such as guide rails and slides, to reduce wear and corrosion of the components. Verify that the hydraulic oil level is within the safe range and add oil in the hydraulic circuit if necessary.
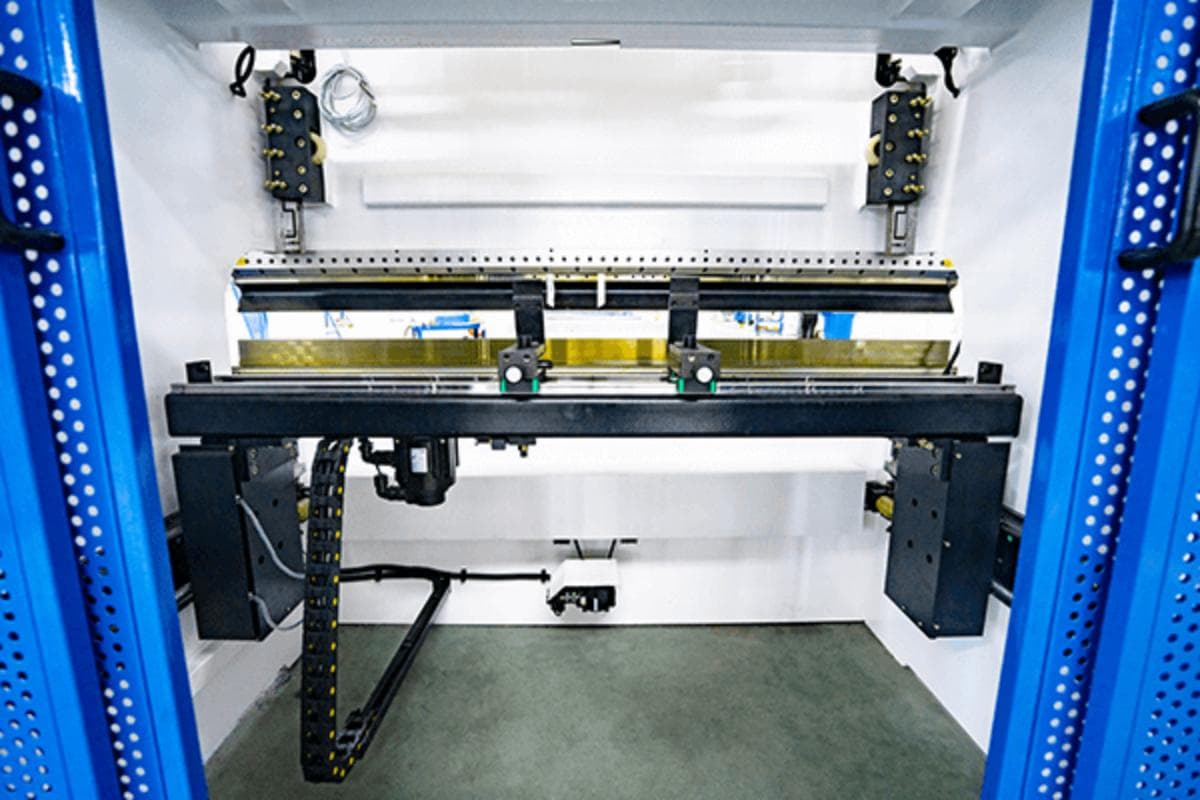
2. Replacing Worn Parts
In addition, when the machine is used for a long time, many components will wear and tear, which can lead to poor operation of the machine, seriously leading to malfunctions and affecting production progress.
Therefore, it is necessary to regularly check the wear level of machine components, especially some moving parts of the press brake, such as guide rails, ram, etc. Inspect the machine for rust, cracks, or deformation.
If no longer in good condition, it is necessary to have professional maintenance personnel replace or repair it. For example, molds, hydraulic seals, valves, and bearings.
Only by investing sufficient maintenance costs can machine performance be guaranteed to be stable, machine service life can be extended, production efficiency can be improved, and machine maintenance costs can be reduced.
3. Safety Precautions
(1) Operational Safety
- Wear Protective Gear: Operators should wear protective gloves, safety glasses, and safety shoes.
- Follow Operating Procedures: Strictly adhere to operating procedures to avoid mishandling.
(2) Equipment Safety
- Install Safety Guards: Install safety guards around the press brake to prevent accidental injuries.
- Regularly Inspect Safety Devices: Regularly check the condition of safety devices, such as laser safety devices and emergency stop buttons, to ensure they are functioning properly.
VII. Conclusion
Building your own press brake is not an easy job, you need to have rich manufacturing experience, and also prepare the necessary materials, tools, and components for press brake build.
A built press brake requires regularly scheduled maintenance to ensure stable performance and longer service life. A well-maintained press brake can save you the cost of repairing and replacing the machine.
ADH Machine Tool is a professional machine manufacturer. Our products include CNC press brakes, fiber laser cutting machines, shearing machines, handheld laser welding machines, and more. Contact us immediately and our team will provide you with the best solution.
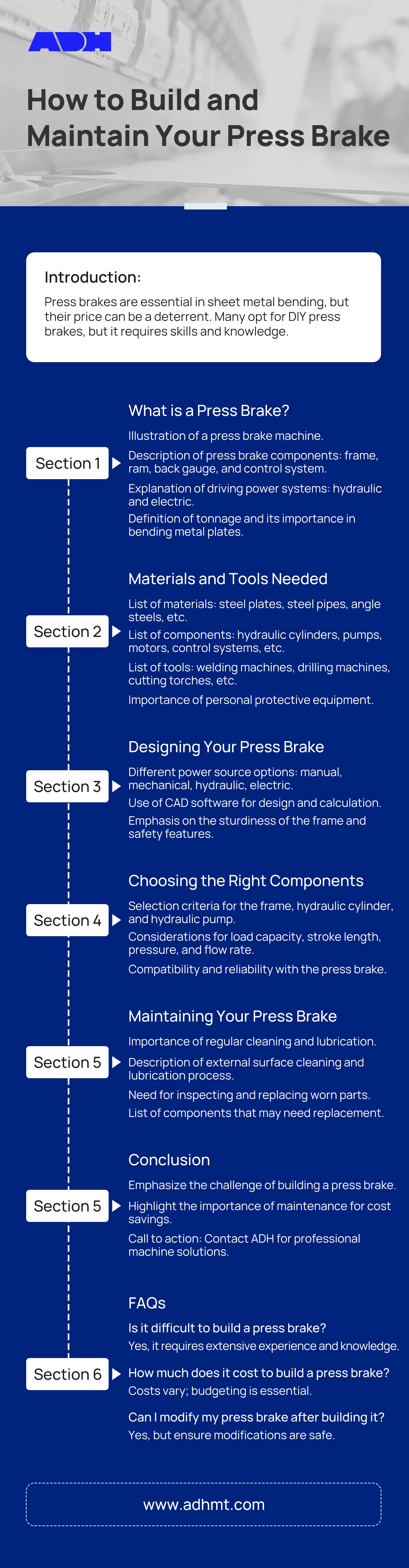
Download the Infographic With High Resolution
Truck Collision Block,Safety Dock Anti-Collision Block,Platform Truck Collision Block,Bumper Guard Strip
Porema (Suzhou) Logistics Machinery and Equipment Co., LTD , https://www.jsporema.com