I. Introduction
Press brakes are indispensable equipment in metal fabrication, and their bending accuracy directly affects product quality and production efficiency. Bending accuracy not only relates to product appearance and assembly precision but also affects a company's brand image and market competitiveness.
However, many factors influence the bend accuracy. My article will start with material properties, bending methods, tooling selection, machine levelling, process parameters and other aspects to systematically analyze the key factors affecting bending accuracy and give corresponding solutions.Â
First, let's watch a video to get a simple understanding of boosting the accuracy on the press brake:
II. Press Brake Parallelism
Various errors can occur when bending sheet metal using a press brake machine, including inaccurate bending radius, insufficient bending force, improper die clearance, positioning error of the back gauge, and errors in bending calculation.
The angle of the workpiece can also deviate from the calculated angle if the press brake is not level or if the CNC crowning mechanism is not functioning properly.
Over time, the press brake's ram and workbench will deform, which can lead to uneven bending and decreased bending accuracy.
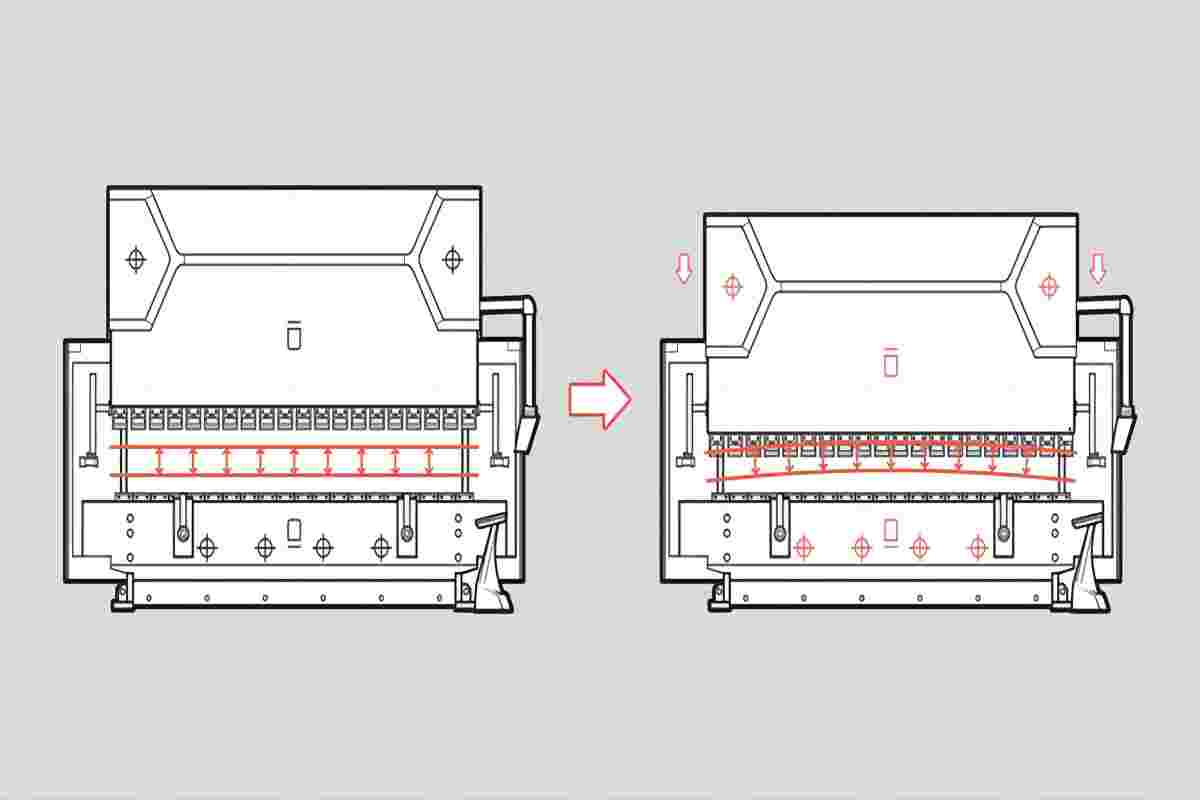
To counteract this, the crowning mechanism must compensate for the deformation of the ram and workbench. There are two types of crowning mechanisms for press brakes: hydraulic crowning and mechanical crowning.
The hydraulic crowning mechanism, found on electro-hydraulic press brakes, compensates for the deformation through the use of hydraulic cylinders on the beam and under the workbench, which generate downward and upward forces respectively.
The compensation force can be adjusted based on the sheet metal thickness, tensile strength, and die opening size, and is controlled by the numerical control system.
Mechanical crowning uses a triangular wedge structure and requires placing two base plates, composed of several wedges, above and below the workbench.
The base plates are connected by disc springs and bolts, and a motor is used to move the wedge relative to the base plates, forming a curve that offsets the original bulge.
In a wedge-style system, the table is designed to bear a certain load depending on the tonnage required. Certain crowning systems provide a programming accuracy of ±0.01 mm and a positioning repeatability of ±0.005 mm.
III. Appropriate Sheet Metal Bending Method
Sheet metal bending accuracy is also influenced by the bending method used. There are three common bending methods: air bending, bottom bending, and coining.
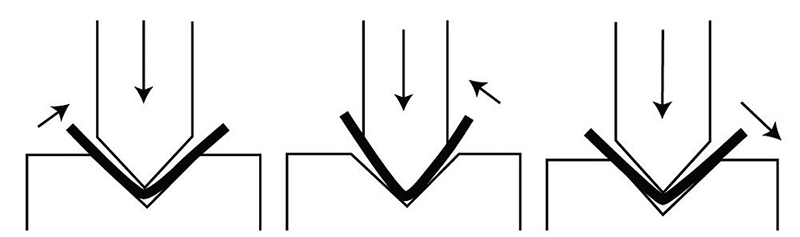
These methods are differentiated based on the relationship between the end die position and the thickness of the sheet metal. The air-bending method does not require full contact between the die and workpiece.
This method requires relatively low bending force, and the punch presses the sheet metal into the U- or V-shaped die, using two points on the die shoulder.
The angle of air bending in press brakes is determined by the shape and stroke of the punch and die, and a proper stroke depth results in more accurate bending.
However, the angle of air bending can change due to the springback after load release, which varies based on the compressive strength of the material.
To modify the angle, some pressure needs to be applied to make adjustments. The bending angle error for air bending is typically around 0.5 degrees. In the bottoming method, the workpiece is positioned at the opening of the punch and V-shaped die.
The size of the V-shaped die opening is 6 to 10 times the thickness of the sheet metal, and the opening size varies based on the desired bend angle and material thickness. The springback of the sheet metal is less after the load is released, resulting in higher accuracy.
Finally, in the coining method, the punch presses the material into the lower die completely. This method requires a high bending force, which can shape the material permanently. The springback after coining is minimal, making this method highly accurate for bending.
IV. Sheet Metal Bending Parameters
In addition to selecting a suitable bending method, it is crucial to determine the bending parameters of the workpiece. During the accurate press brake bending process, the inner surface of the metal undergoes compression while the outer surface is stretched.
To ensure the accuracy of the bend, it is necessary to know the tensile value of the material and calculate the minimum flange tolerance length. The parameters involved include the press brake bend radius, K factor, bending deduction, bending allowance, sheet metal setback, etc.
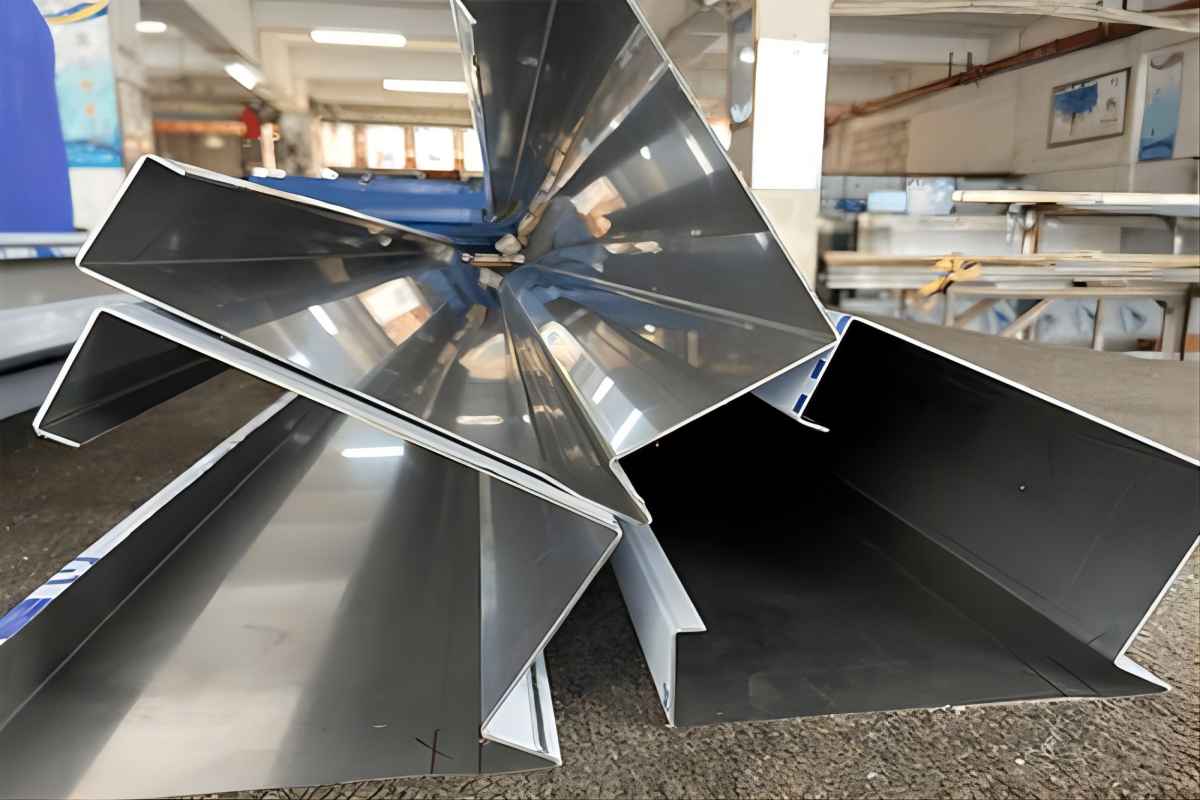
V. Material Properties
If the material properties are inconsistent, the angle of the workpiece may vary when using air bending. This is because different material properties affect the stress state of the workpiece during the bending process.
From a mechanical perspective, the bending process essentially generates compressive stress on the inner surface of the workpiece and tensile stress on the outer surface, causing plastic deformation of the workpiece. Material performance parameters such as yield strength, elastic modulus, and elongation all influence this stress process.
Generally speaking, the higher the yield strength, the stronger the material's ability to resist deformation. Under the same bending force, the bending angle will be smaller; conversely, the lower the yield strength, the easier the material deforms, and the bending angle will be larger. The elastic modulus affects the amount of springback after bending. The larger the elastic modulus, the more obvious the springback, which will cause the actual bending angle to be smaller than the die angle.
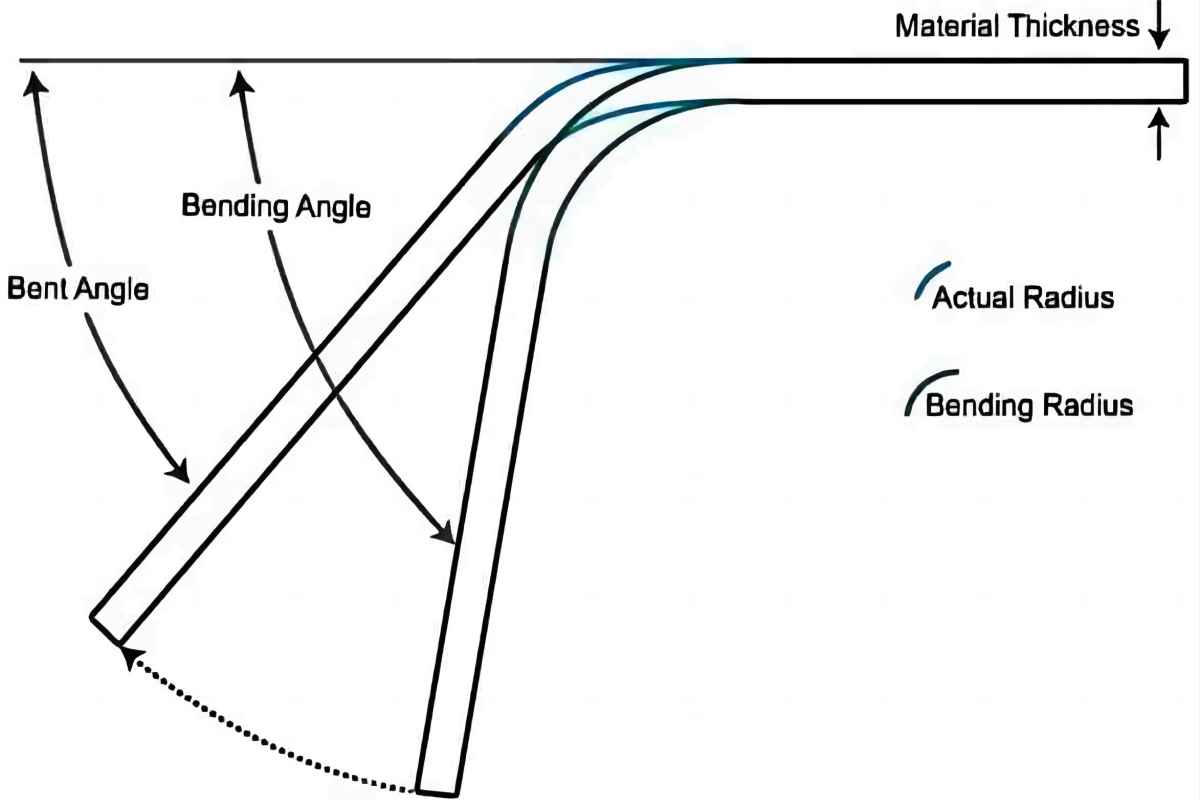
Additionally, if the plate thickness remains the same but the die opening narrows, the bending angle of the workpiece will change even more. This is because narrowing the die opening is equivalent to reducing the bending radius, which will cause the material to undergo greater deformation in the bending area, and the stress will be more concentrated, making it more sensitive to material properties.
It's important to note that even though the nature of the material may be inconsistent, they may still fall within the thickness and strength tolerances of the mill. This is because the tensile strength of many materials falls within a certain tolerance range.
Another factor to consider is the outer surface of the sheet, as different natural texture directions require different bending pressures. It's crucial to keep in mind that these values may not be the most precise, so adjustments to the angle and length may be necessary during bending.
VI. Press Brake Balanced Operation
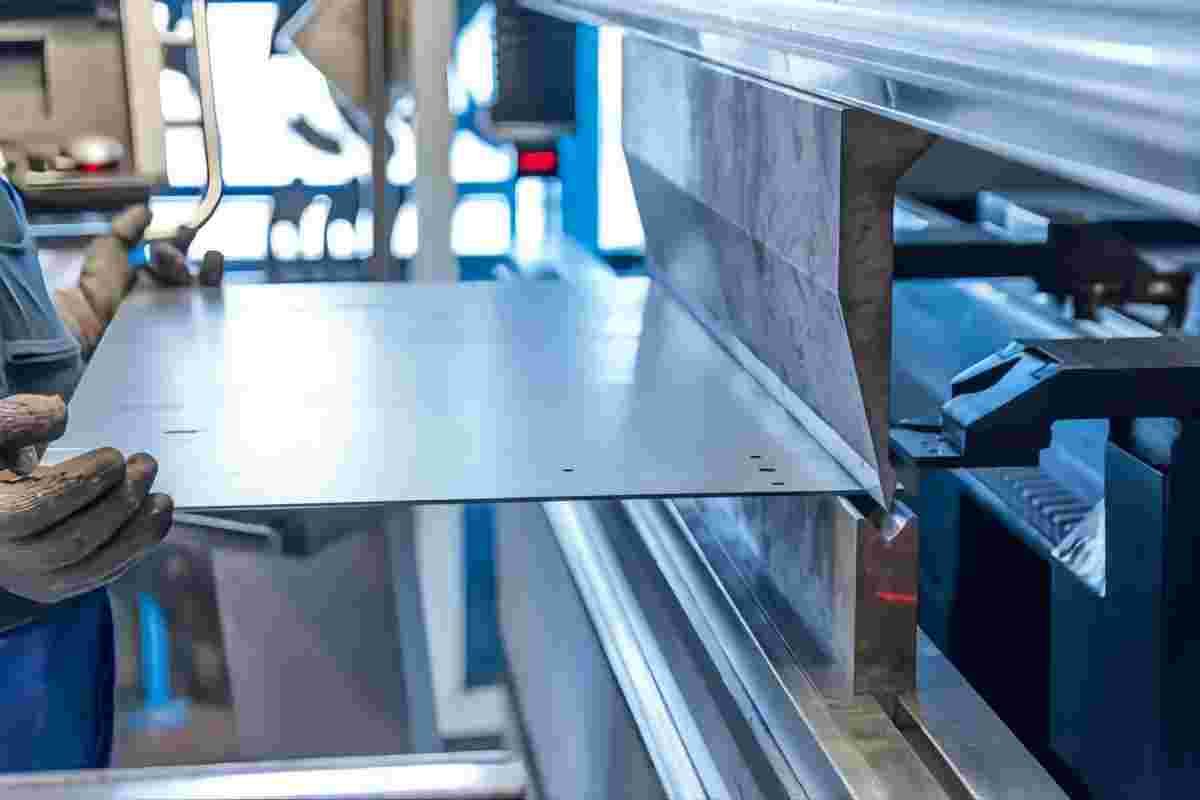
For smooth and precise bending, it is necessary to balance the precision press brake. The specific operation process is as follows:
- The intermediate frame of the bending machine should be supported on a sturdy bearing surface and clamped at one end while being supported at the other end.
- During the bending operation, the lower two supporting claws of the press brake should be made to touch the workpiece's supporting surface evenly and then locked into place.
- The upper cover should then be tightened, and the position of the upper support claw should be adjusted until it is properly secured.
- It is important to ensure that all the supporting claws of the intermediate frame are applied evenly throughout the process.
- To avoid wear on the workpiece surface, a layer of pure copper sheet or fine emery cloth should be placed between each supporting claw and the supporting surface of the intermediate frame.
Modern press brakes are designed to ensure bending accuracy. By following these steps, the sheet metal machine can be balanced and run smoothly.
VII. Suggestions to Improve Bending Accuracy
1. Regularly calibrate the bending machine to ensure the accuracy and stability of the machine. Calibration contents include: coaxiality of upper and lower dies, parallelism of sliders and worktable, backgauge dimensions, etc. The calibration cycle can be determined according to the production rhythm and workpiece accuracy requirements.
2. Reasonably select bending process parameters. According to material properties and product geometric dimensions, choose the appropriate bending method (air bending, bottoming or coining), and match the corresponding V-die opening width and die radius. Accurate bend angle, bending force and bending times also need to be calculated and process verified.
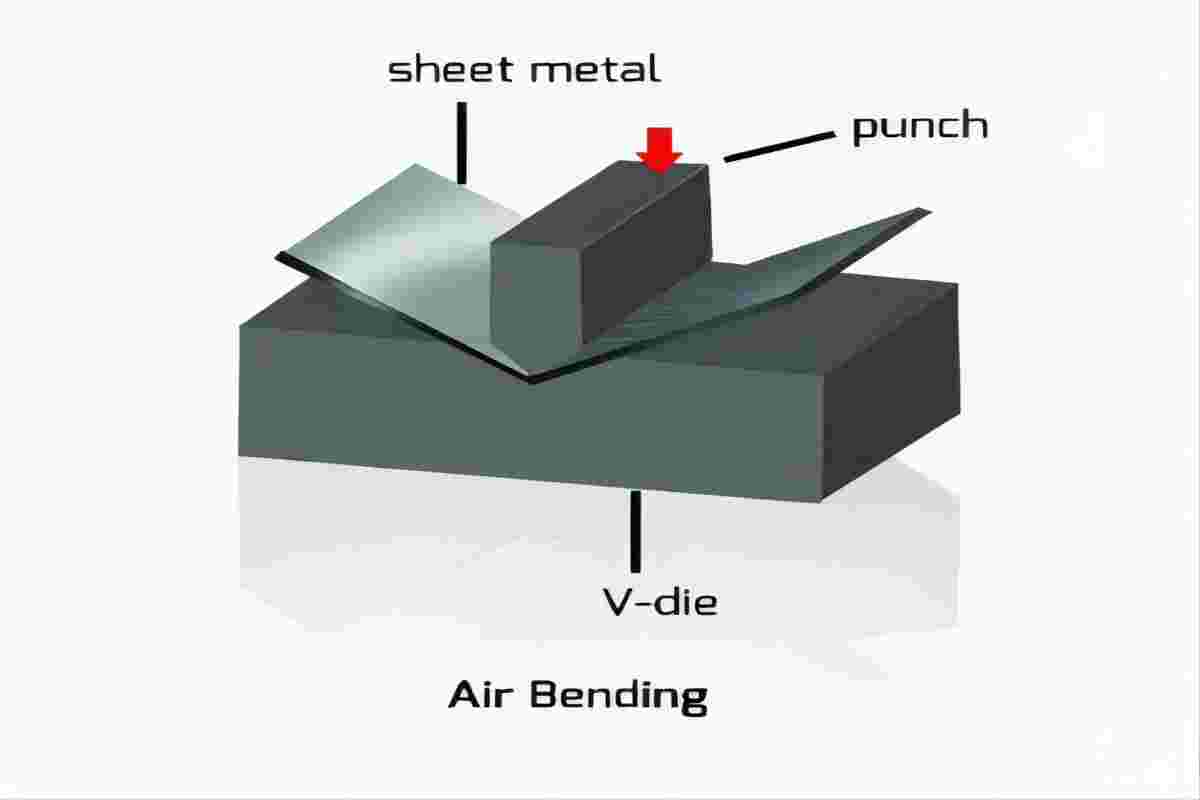
3. Optimize the die structure design. The die is one of the key factors affecting accuracy of the finished product. The die surface should have uniform hardness and low roughness, and undergo special surface treatment to reduce friction. Rationally design the shoulder radius of the female die to avoid cracking caused by stress concentration. Adopt a segmented or multi-wedge beam structure to achieve local pressure compensation.
4. Improve the machine balance adjustment mechanism. A multi-point synchronous balance compensation device can be used to actively compensate for machine deformation by independently controlling multiple pressure points. Upgrade the CNC system and introduce closed-loop feedback control to adjust the balance pressure automatically.
5. Strengthen process quality monitoring. Introduce online measurement in the bending process to monitor the bending angle and dimension in real-time. Perform statistical analysis on the measurement data and promptly adjust the bending parameters when the deviation trend is obvious. Establish a product quality traceability system to ensure every bent part has a traceable record.
VIII. Conclusion
This article presents various ways to solve the accuracy of press brake bending problems for press brake manufacturers in the metal forming and fabricating industry. These methods include the selection of bending method, the leveling and compensation mechanism of the machine, the choice of bending materials, and the precision bending parameters.
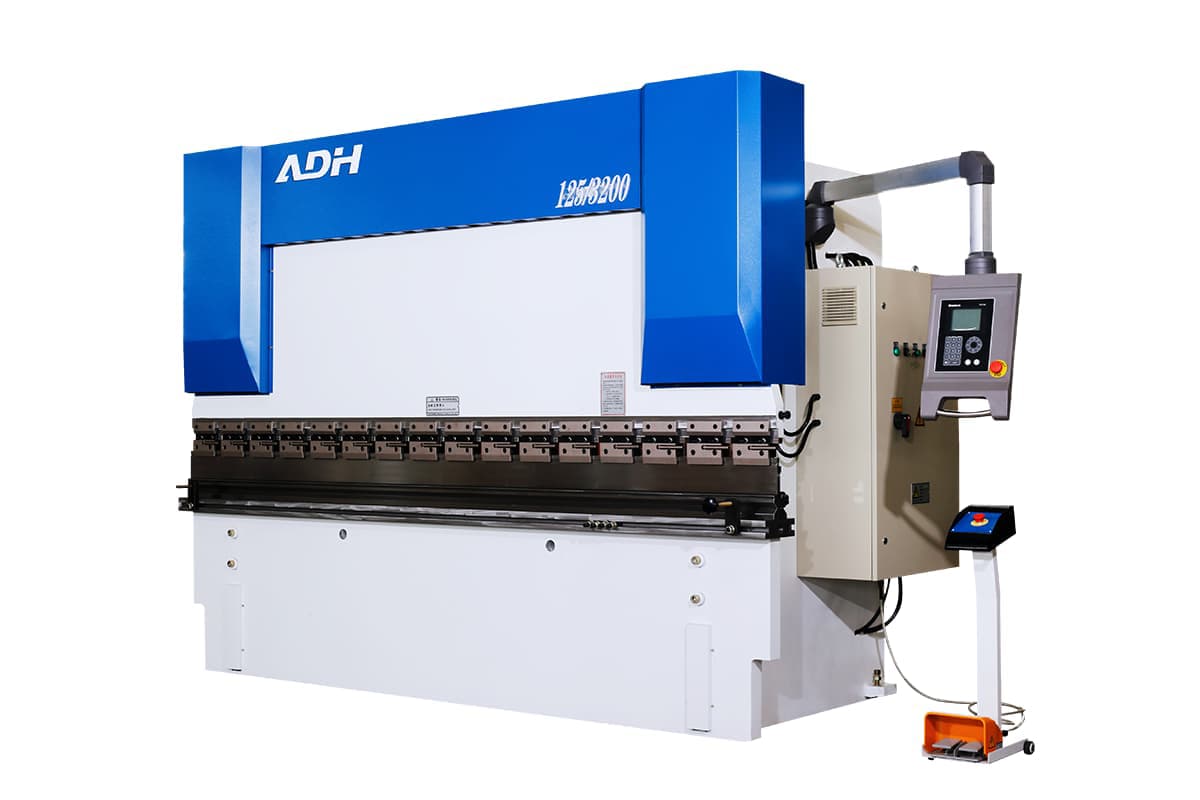
ADH Machine Tool is a sheet metal processing machine manufacturer for processing press brakes, shears, and fiber laser cutting machines. ADH press brakes adopt advanced hydraulic servo systems and electric proportional valve technology, allowing precise control of bending force and speed and ensuring the consistency of bending angle.
The machine is equipped with high-precision grating rulers and angle sensors, which can detect the position of the upper die and the bending angle in real time, ensuring a position repeatability of ±0.01mm and an angle repeatability of ±0.1°.
To learn more about our press brake, you can browse our product page or get in touch with our product experts.
Vacuum Block-Moulding Machine,Polystyrene Block Machine,Vacuum Block-Moulding Machinery
Hangzhou Sutuan Machinery Co.,Ltd.
Leading EPS EPP ETPU machinery manufacturer , https://www.sutuanmachinery.com